Pushing the Boundaries of the Invisible
Nanometer-scale 3D printing refers to the capability to fabricate objects at the nanoscale. To fathom such diminutive dimensions, consider this—1 nanometer is a mere one-millionth of a millimeter. By comparison, the diameter of human hair is a more comprehendible 75,000 to 100,000 nanometers.
A New World of Minuscule Might
Immersed in exciting potential, nanoscale 3D printing heralds industry-altering advancements, promising everything from tinier computer chips and integrated circuit boards to nanometric metal components poised to heighten batteries with rapid charge and discharge capacities.
Such breakthroughs are set to soar in efficiency and multiply the productivity of smaller components.
Sectors like microelectronics, nanorobotics, and sensor technology stand to gain immeasurably from the ability to create with precision at the nanometer scale, unimpeded by any sacrifice in accuracy. Universities across the United States are at the vanguard, probing diverse printing methods tailored to industry-specific preciseness.
In particular, institutes dedicating their prowess to electrical advancements are uncovering new territories as are those fine-tuning nano-printing techniques harnessing photochemical reactions for applications like immobilizing proteins, polysaccharides, or genes.
Materials synthesis and plastics, historically benefitting from printability at this scale, have only recently witnessed metal object printing breakthroughs with nanometer fidelity over the past two or three years.
This superlative precision in metal 3D printing at the nanoscale empowers scientists to assemble objects atom by atom.
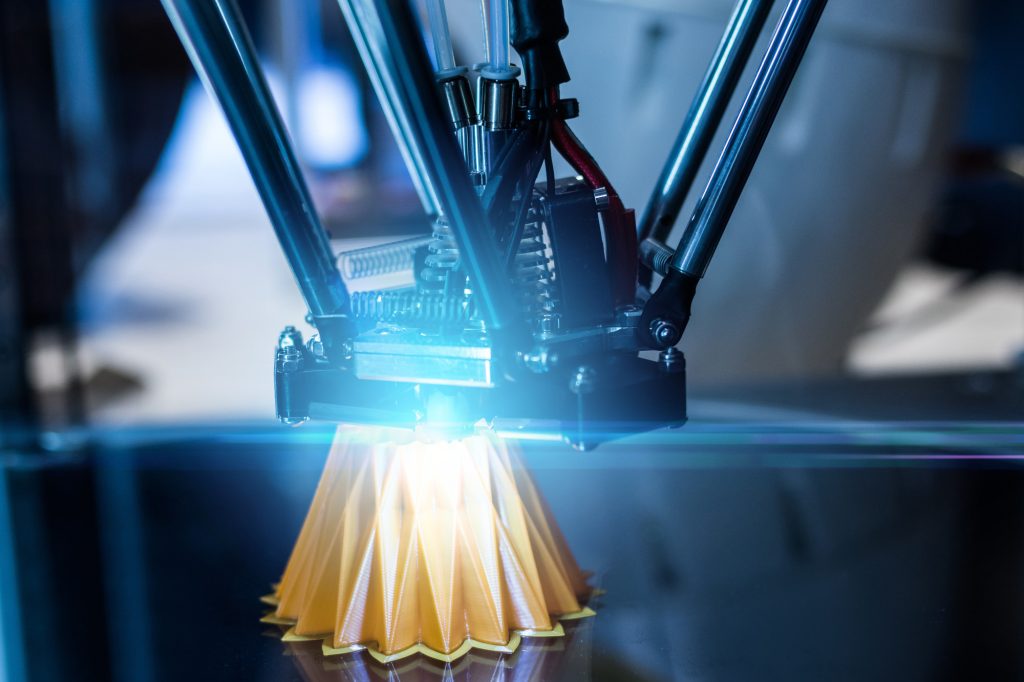
Solutions Taking Shape on a Nanometric Canvas
The pioneer at the Institute of Chemistry, Doctor Dmitry Momotenko, heads a primary research group that envisions 3D printing batteries with charging and discharging speeds surpassing current technologies by over a thousandfold. “Imagine electric vehicles charging within seconds if today’s science could permit it,” he opines.
The goal is a reduction in the distance ions travel within batteries. Nano 3D printing paves the way for his team to reexamine ideas decades old, aspiring to print internal battery structures that permit electrons to traverse the entirety of the battery instantaneously, instead of navigating from one cell side to the next.
Microelectronic advancements, like the precision printing of metal structures down to 25 micrometers and anaerobic nanobots (nano-level microchips), can similarly leverage this technology.
Crafting Precision at the Core of Nano-Level 3D Printing
Chemist Liaisan Khasanova from the University of Oldenburg is on a quest to engineer special nozzles indispensable for nano-level printing. The process starts with an ordinary quartz glass tube, introduces a 1-millimeter capillary, and bathes it in blue liquid. When electrified, a reaction sparks a resounding burst. Post the rupture of the tube, a sufficiently miniature orifice emerges that meets their demanding specifications.
“In the belly of the device, a laser beam heats and stretches the tube. A sudden increase in pull force causes the glass to break midway, yielding a supremely sharpened tip,” explains Khasanova, a doctoral candidate.
Back in the university’s Wechloy lab, precision printers build and program to stringent standards, bearing resemblance to their domestic counterparts but differing in the fine extent of their output.
These printers’ operation rests on solid granite bases lined with foam to diminish any vibrations incurred during printing—key to achieving higher accuracy at reduced scales. This represents a stark contrast to conventional powder-based metal 3D printers, which only achieve resolutions at the micron level—1000 times the difference.
Even laboratory lighting doesn’t escape scrutiny due to potential electromagnetic disturbances, prompting a switch to battery-powered illumination to insulate against AC-generated electromagnetic fields.
Observing the Minute Majesty of Metal Nanostructures
Nanometer-level printing’s ease with plastic polymers—a lack of the requisite strength and lower thermal resistance—facilitates simpler structural formation. The plasticity of these materials has spearheaded much of the technology’s most recent advancements.
In contrast, metal nano-level 3D printing demands stricter tolerances, alongside heightened thermo-tolerance and wear-resistance. These printers breed innovations, ranging from advanced print algorithms to reimagined nozzle tips, enabling precision crafting at minute scales.
Thus far, the team is adept with metals like copper, silver, nickel, nickel-manganese, and nickel-cobalt alloys. Dr. Momotenko’s research has culminated in copper spiral pillars measuring just 25 nanometers—or 195 copper atoms—as presented in their study, printed one layer at a time, each a few nanometers per second.
The Lifesaving Sprint of Time
Printing flat spiral objects augments battery storage and production, governin.xticksf the nanometric structure for swift and even traversal of protons through a battery, enhancing charge and discharge rates.
This boon benefits sectors reliant on energy storage, from electric vehicle batteries to off-grid homes and data server farms with a steadfast aim to never go offline due to grid failures.
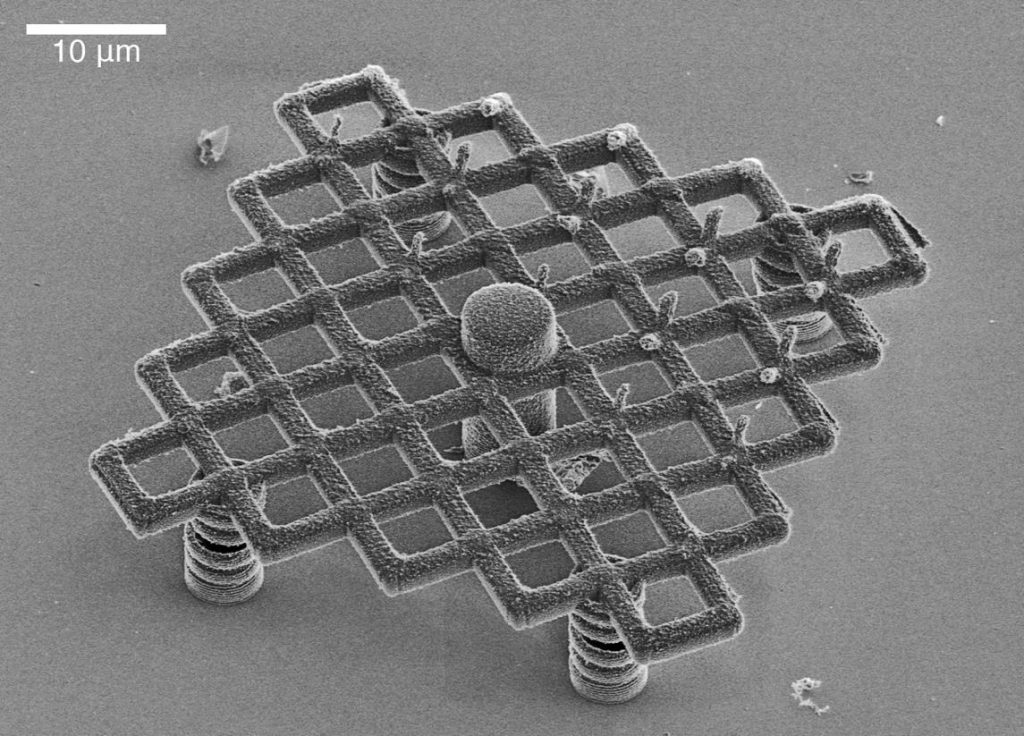
The First Hurdle: Managing Risks
To minimize risks associated with lithium-ion battery production, a specialized sealed chamber filled with positive pressure inert argon gas was devised. The chamber, large enough to house the printer within an inert atmosphere, addresses thermal management during battery charging.
On the one hand, Dr. Momotenko says, is the chemistry required to produce nanoscale active electrode materials. On the other, is adapting the printing technology to accommodate these materials.
Then Comes Progress
With existing electroplating techniques, the method boasts positively charged copper ions and negatively charged electrodes within a solution. In stark contrast to micrometer-restricted powder-based 3D printers, electroplating enables the team to venture into nanoscale 3D printing.
Battery technology may be the first of many applications. Dr. Momotenko also harbors bolder concepts—from harnessing the nascent field of spintronics aimed at manipulating electrons’ quantum mechanical characteristics, “spin,” to manufacturing sensors capable of detecting single molecules, pivotal in identifying diseases like Alzheimer’s notorious for their trace biomarkers.
Even after development, the team holds a sense of awe for their power to create what remains unseen to the naked eye.
Discussion about this post